The formulation of the process specifications in the shaft parts is directly related to the quality of the workpiece, labor productivity and economic benefits. A part can have several different processing methods, but only one of them is more reasonable. In the process of formulating the machining process specification of the shaft parts, it is necessary to understand the structural characteristics, precision, material, heat treatment and other techniques of the parts. Requirements, and study product assembly drawings, component assembly drawings and acceptance criteria. For casting axes that need to be machined on all surfaces, the minimum surface is corrected according to the machining allowance. And choose a smooth surface to allow the gate to be opened. Select a solid and reliable surface as a rough reference, while the coarse reference is not reusable.
Rough reference selection: For non-machined surfaces, non-machined surfaces should be selected as the rough reference. In the machining practice class, the machining of shaft parts is the most basic and important project for students to practice turning skills. However, the quality of the finished workpieces of the students is always unsatisfactory. After the analysis, the students mainly analyze the process of the shaft parts. The formulation of the process rules is not reasonable enough.
Whether the process regulations are properly formulated directly affects the quality of the workpiece, labor productivity and economic benefits. A part can be manufactured in several different processing methods, but under certain conditions, only one method is more reasonable. Therefore, in the processing of shaft parts, in the formulation of the process rules, it is necessary to proceed from the actual situation, according to the specific conditions of equipment conditions, production types, etc., as far as possible to adopt advanced processing methods, to develop a reasonable process.
The processing route of carburizing parts is generally: blanking→forging→normalizing→roughing→semi-finishing→carburizing→carbon removal processing (for parts without hardness)→quenching→threading, drilling or milling→ Rough grinding → low temperature aging → semi-finishing → low temperature aging → fine grinding.
Fine benchmark selection: To meet the principle of baseline coincidence, choose design basis or assembly benchmark as the positioning benchmark. In line with the principle of benchmarking. Use the same positioning reference as much as possible in most operations. As much as possible, the positioning reference coincides with the measurement reference. The selection of high precision, stable and reliable surface is a fine benchmark.
. Http://news.chinawj.com.cn Editor: (Hardware Business Network Information Center) http://news.chinawj.com.cn
1.Automatic continuous feeding, unlimited length, improve production efficiency and reduce production costs.
2.It adopts numerical control, running information and status feedback in time, and the operation is simple.
3.The use of numerical control program adjustment ensures the machining accuracy of the workpiece.
4.Hydraulic clamping of the material, smooth operation, to ensure the processing accuracy of the workpiece.
5.The device is simple and convenient to operate, safe and reliable in performance, and high in production efficiency.
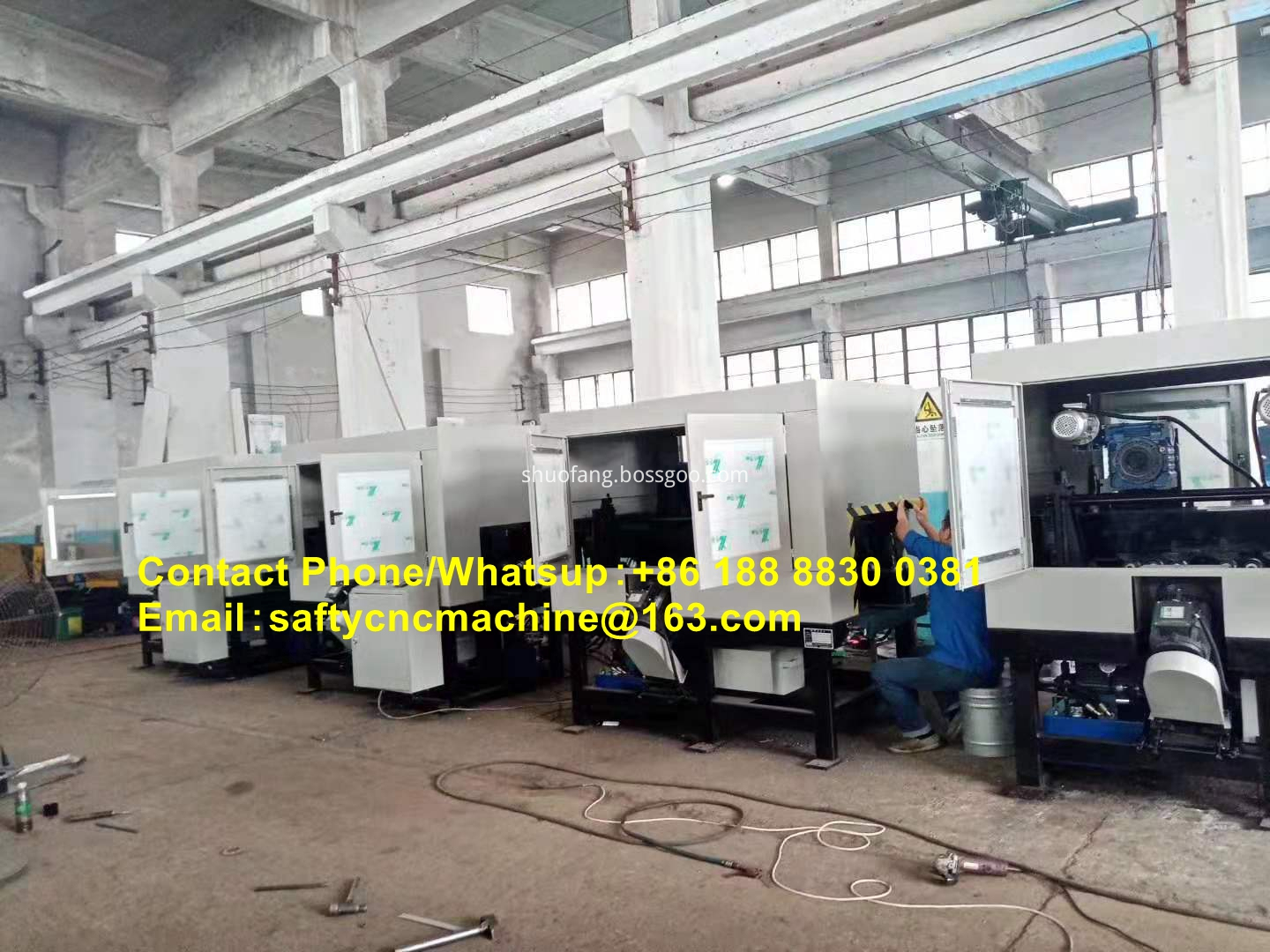
Heel Milling Machine,Milling Machine for Angle Steel Heel,Angle Steel Heel Milling,Steel Angle Milling Machine
Shandong EN FIN CNC Machinery Co., Ltd , https://www.sdfincncmachine.com