The packaging of LED explosion-proof lamps has different specifications and models depending on the location of the glue, the color of the LED bulb, the size of the LED lamp, and so on.
1. First look at the location of the explosion-proof lamp glue application:
a, if you apply glue to cover the lamp beads, you must choose transparent silica gel with high light transmittance, and it is recommended to extend the cover cover time;
b. If your gluing position does not cover the top of the lamp bead, but only acts as a potting next to the lamp bead, or if it is bonded to the outer PC shell or glass cover, it is recommended that you check the interior of the lamp bead Encapsulation glue, see if the encapsulation glue becomes turbid, discoloration, etc. This situation is generally caused by the unqualified quality of the encapsulation glue of the LED chip. The silicone material containing phenyl is used. When the aging is sealed, the phenyl is oxidized. ;
c, do you often see some high-power lighting burst, so furniture choose explosion-proof lights.
2. Secondly, LED explosion-proof lights usually use different colors according to the environment of use, to achieve the effect of rendering the environment by rendering different colors:
At this time, it is necessary to focus on the comparison of colors, and choose the one with high color rendering: the color rendering of objects with color rendering is true when the light is irradiated, the value is 0-100, and now the color rendering specifications of LED bulb explosion-proof LED lamps are more than 75, but up to People advocate that it is better to choose more than 80. People who have studios in their homes should buy bulbs with high color rendering, which can better reflect the authenticity of colors;
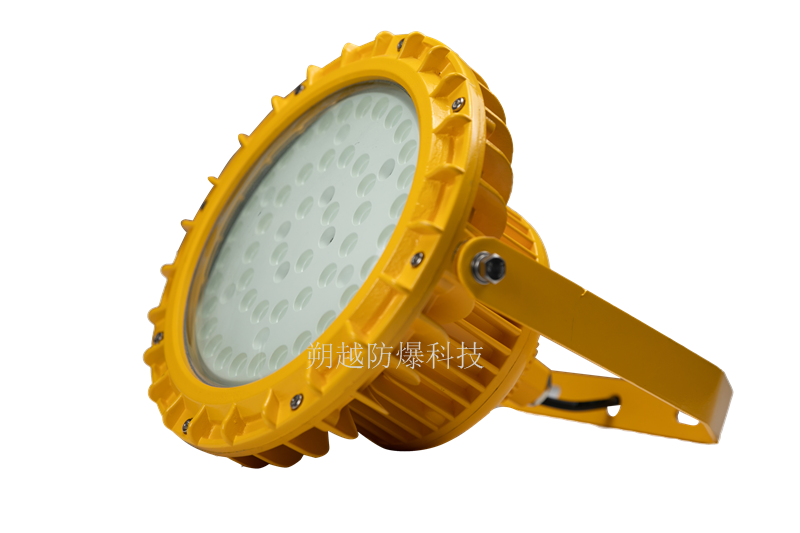
3. In addition, the size of the explosion-proof lamp is also an important factor in choosing which encapsulant to use:
a. The air permeability and hardness of the glue affect the reliability of the LED. The viscosity of the glue directly affects the speed of the phosphor sinking. Generally, it is divided according to the size of the LED. The smaller the size, the higher the hardness, and the larger the size, the higher the viscosity. , Silicone package with low hardness;
b. Generally, companies will use silicone and silicone resin (herein collectively referred to as silicone) as the encapsulant for LED lamp beads, but because of its certain moisture permeability and oxygen permeability, especially in high temperature environments, sulfur, oxygen, Elements such as bromine can easily penetrate the silica gel and enter the LED lamp bead package.
Enterprises generally use the following methods to solve the problem of the brightness of the bulb deep into the bulb and which bulb you choose:
Method 1. Hard silicone package:
At present, most LED packaging factories use higher hardness silicone as the LED lamp bead encapsulating material can delay the blackening time, but the stress problem caused by the higher hardness of the ancient cross has increased the internal structure of the LED lamp bead package. Reliability risk. In the case of thermal expansion and contraction, the bonding wire inside the LED lamp bead is easily broken to cause functional failure. However, even if silica gel with higher hardness is used, the glass transition temperature of silica gel is only 50-70 degrees Celsius. At high temperatures, the molecular structure of silica gel becomes larger, and sulfur, oxygen, bromine and other substances can easily enter. The LED package reacts with the silver plated layer.
Method 2. Apply organic gas barrier material on the surface of silica gel:
Therefore, many LED packaging factories still use a softer silicone, coating a layer of organic lease material on the surface of the LED lamp bead package, which can delay the blackening time and avoid the stress of the silicone that is high in Yining. problem.
It is not difficult to see that the use of higher hardness encapsulant or surface coating organic gas barrier material, these two methods to solve the blackening problem are only improved on the front channel of the colloid, other channels are still bought to block, sulfur, oxygen , Bromine and other substances easily enter the LED lamp bead package, these two methods are very poor. What's more, it is coated on the surface of the LED lamp beads, and the organic gas barrier layer is easy to be worn in the later processing. At the same time, organic gas barrier materials are prone to degradation and molecular cracking and cracking under high temperature environment for a long time, and they still cannot provide effective protection.
Method 3. Apply organic gas barrier material to the silver coating:
Due to the decision of the SMD LED structure, it is quite difficult to block the 2 and 3 channels, which is also the technical bottleneck of the current LED packaging industry. Blocking the channel is more difficult and difficult. To effectively solve the blackening problem, only the surface of the silver layer can be completely protected. Some LED packaging factories coat organic gas barrier materials on the surface of the silver plating layer. Even if the channel is not blocked, sulfur, oxygen, bromine and other substances can not react with the silver plating layer when they enter the LED package.
However, the thickness and consistency of this organic gas barrier material is difficult to control. The important thing is that the organic material is easy to explain in a high temperature environment for a long time, molecular fission occurs, and the organic gas barrier layer cracks, and ultimately it does not provide good protection. .
Method 4. Semiconductor solutions:
The semiconductor adopts advanced, cutting-edge and unique PPL technology to solve the blackening problem. It takes advantage of an inorganic substance on the surface of the silver plating layer. The inorganic substance has excellent compactness and effectively blocks sulfur, oxygen, and other substances from the silver plating layer. reaction. At the same time, it has long-lasting and stable chemical properties. It is very outstanding in the upstream of corrosion resistance and high temperature resistance. It completely solves the blackening problem caused by sulfidation, oxidation, and bromination. The vulcanization test is 40% higher than that of ordinary products.
Of course, the technology of LED explosion-proof lamp encapsulant still needs continuous improvement. I believe there will be more and better improvements proposed and promoted.
Smart Light,Smart Lamp,Rgb Light Bulb,Smart Led Lights
Guangdong Smart Street Lighting Co., Ltd , https://www.fldlight.com